Stories
1
2
3
4
5
6
7
8
9
10
Then I had to go to a machine shop to have a hole punched in the flat plate and the rod welded into it perfectly vertical. Then to drill a hole in the exact center of a plywood circle
with sheet metal sides, to insert the protrusion and the shaft had to be wired in exactly vertical before pouring the concrete
The weight was on the bottom of the shaft and the throwing head was 30 inches above so that kicking the wheel could cause the head to wobble unless the upper bearing was attached to a strong frame. The idea was to use four vertical 2x4s on either side as the frame, to hold the seat, top bearing and work table. The lower bearing sat in the middle on a 4x12 which was attached on each end with lag bolts to 2x4 lower side rails making an H shape. I retained the 4x12 but replaced it in later models with two slotted 4x4s forming an X, so that the lower rails were bolted in front and back instead of the middle. To secure the 2x4 up-rights at the bottom, I slotted the up-rights between two horizontal 2x4s giving me stability forwards and back. At about twelve inches in height I ran another slotted 2x4 horizontally on either side, which added front and back stability and acted as steps to mount the wheel and to stand on while throwing if one desired. One did not want to step on the wheel itself.
The problem of stability was crosswise, where the top could move from side to side. Between the four vertical 2x4s in the rear I bolted the seat made of 2x10 fir or redwood.
(4 of 10)
Next Page
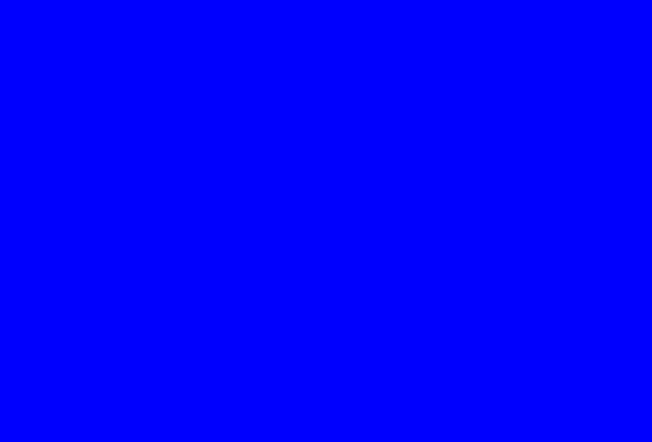