Stories
1
2
3
4
5
6
7
8
9
10
Meanwhile someone with a truck helped me move the wedging table and twenty foot long work table I had built at a wood shop Wherebe had had on Virginia Avenue, over from Wherebe's now abandoned pie-in the-sky store-front pottery shop on San Jose Avenue. We left the huge shelf complex I had built thinking it was too big for the two car garage.
I decided to design a potter's wheel using two by fours. I used the wheels already there as a guide. The essence of it was a cement wheel which was about twenty-eight inches in diameter and could be anywhere from two to five inches thick. I would have to pour my own wheels and acquire three-fourths inch thick shafts of cold-rolled steel about 30 inches long. This I quickly found to be inadequate, since the shaft had a tendency to bow and cause the aluminium wheel head to wobble. I would be using a four inch thick concrete kick wheel which weighed maybe two-hundred and fifty to three hundred pounds. This gave a long lasting spin. To this shaft would need to be welded a three inch wide and 26 inch long flat iron, such that the shaft would protrude through one inch on the bottom and would fit into and sit on the bearing. Then I would need to acquire a 28" diameter plywood perfect circle as circumference mold and make a sheet metal siding mold strong enough to hold the cement.
There was a problem buying cold rolled steel as they had a minimum limit, so I had to buy it out the back door so to speak from the workers in the back, who would get it in exchange for money or perhaps even liquor.
(3 of 10)
Next Page
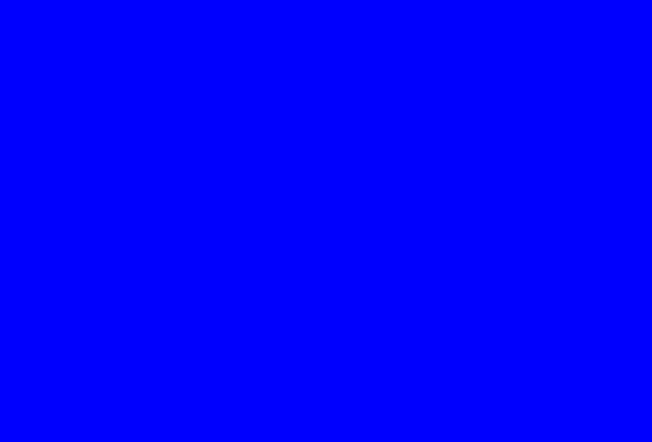